For Cleaner and Greener Production
In the production and particularly in fiber cement industry, environmental preservation and clean production system are the basic factors for long term and sustainable development. For NAVIFICO, improving the production environment to ensure safety and health for workers as well as upgrading machinery, improving productivity, increasing business efficiency have caused a dual effect: both quality assuarance and keeping environment friendly.
NAVIFICO’s fiber cement products are manufactured by wet process, closing from preparation of raw materials to finished products. Due to the specific process, the partical size of materials which are very fine, easily dispersed in the production area, so the preparation of raw materials stage is important in protecting the workers and environment. At this stage, there are three kind of raw materials mainly water, pulp, cement and fiber. As the result of being fully invested at this stage, the most critical stage, NAVIFICO’s roof sheets quality have been very stable, good appearance, high strength and resistance to water absorption. Followings are the outline of the production stages in which the materials were processed in an automatical, self-contained and continuous line.
Wasted kraft paper are soaked in water in one day before being processed. Wasted water is pumped through filters and being treated by chemical for reuse in the process. After soaking in the water, kraft paper was put through pulper , separating impurities, refinering fibers in the form of cellulose slurry, then it is contained in a closed storage tank. Cellulose slurry was dosed and pumped into the mixer. In such the cellulose preparation, the process keeping dust arising under control, reusing waste water for the next cycle of production.
Cement is transported by road tanker from cement plants to the factory and was pumped directly to the cement tank. From the tank, cement is weighted and fed directly and automatically into the mixer. Thus, at this stage, cement dusts generated are also controlled.
Fiber reinforced materials are sealed in PP bags, so when the bag covers were torn, dust can be spread. NAVIFICO has designed and fabricated a system in which the PP bags were torn in a closed room and the fibers were disintegated automatically. The fibers were processed in damp condition, stirring with water as a slurry then were pumped to the mixer. Thus, the fiber dusts were controlled in a wet process. This is a special equipment at NAVIFICO keeping the environment clean and safe.
After raw materials preparation stage, the mixed slurry was stock and fed to sheet machine (Hatschek machine) where the number of layers in the sheet to be produced. This process is also in the wet condition mainly slurry, so dusts are not generated in the air. All the backwater from the sheet production is collected in a channel underneath the sheet machine and pumped into the clarifying cone where the solids are separated and the pure water flows over into the production process. Only a small amount of waste water released from the production, is filtered by chemical methods and feeding into production. Next stages are cutting, corrugating and precuring. Finally, the depiler separates the mixed stack to a pile of finished product and the steel molds back for the next production cycle. The finished products are air cured and keeping humid during three weeks before delivering to the customers.
Cement cone and mixer
NAVIFICO’s vision is business benefits for both the company itself and the community. The company has invested and upgraded equipment: automatic bag tearing and raw materials disintegators, cellulose pulper and refiners, press section with thickness measurement. Renewal of precuring tunnel, handling system and boilers. In particular, new piler, depiler system and mold cleaning has also helped increasing productivity. Consequently, the Company products are conformed to corrugated fiber cement standards such as breakload, impermeability, product loss ratio. Increasing in productivity, leading to increase quality, cost effectiveness, at the same time, increasing the competitiveness of products on the market.
In terms of product diversification, the production line can produce PVA fiber cement (Polyvinyl Alcol) when it is modified and added some equipment. The company has made sample trial product with synthetic fibers from 1998 and being the first company in Vietnam producing PVA fiber cement corrugated sheets for roofing. The company provided PVA fiber cement roofing for housing projects in Soc Trang Province, a project to improve and reserve the coastal mangrove areas which is supported by World Bank.
Furthermore, while investing in machinery and equipment, leading to a better production environment and keeping safety for workers and the community. The results checked by Health Center of Labor and Environment of Ho Chi Minh City on 7/8/2006 at NAVIFICO showed that dust concentration in raw material preparation area is 1.1 mg/cm3 – getting the standard that permitted the level of 4 mg/cm3. Furthermore, the company has also coordinated with local authorities and organizations to carry out general health care for all workers, timely detect and treat for them.
The company has interested in environmental issues, meeting the requirements of the government in fiber cement industry, meanwhile, has also been known in terms of technical improvement. These two factors are the advantages of competitiveness in the marketplace. In the Quarter 4 annually, when the dry season in Vietnam comes, is also the high sale season for roofing. NAVIFICO, with strong points on productivity, cost production , product quality and sales network which is built and covers all the southern provinces of Mekong Delta River and the Central Region of Vietnam, has the opportunity to maintain and expand its markets.
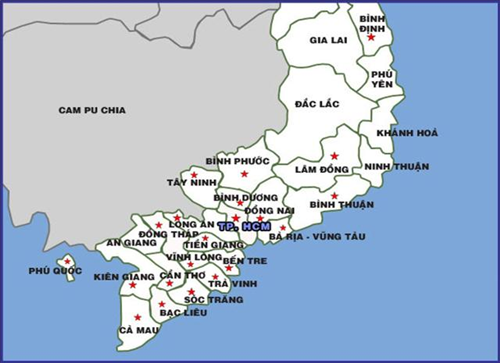
Sale Network
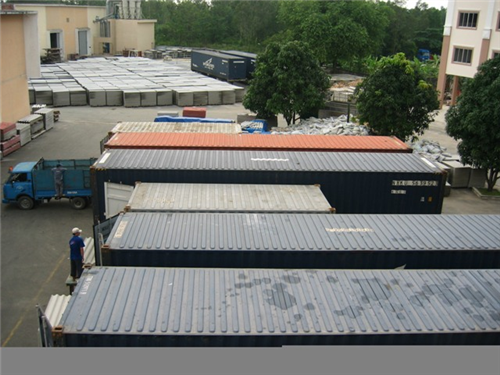
Exporting products